Recyclage des plastiques : cap sur les nouvelles technologies
L’enjeu est aujourd’hui partagé par tous, partout dans le monde : il est urgent d’accélérer l’économie circulaire du plastique pour réduire son impact sur la planète. Le recyclage est l’une des solutions. En 25 ans, le recyclage dit mécanique a fait ses preuves, en permettant la création de filières : PET, PEHD pour les bouteilles et flacons. Mais pour les emballages plus complexes, les pots, barquettes ou films, il atteint ses limites. Pour les recycler, de nouvelles solutions émergent et seront présentées lors du Forum de rencontres internationales organisé par Citeo et EEQ, les 4 et 5 février.
Carlos de Los Llanos, Directeur scientifique de Citeo, nous éclaire sur les enjeux et les perspectives qu’ouvrent ces technologies d’avenir.
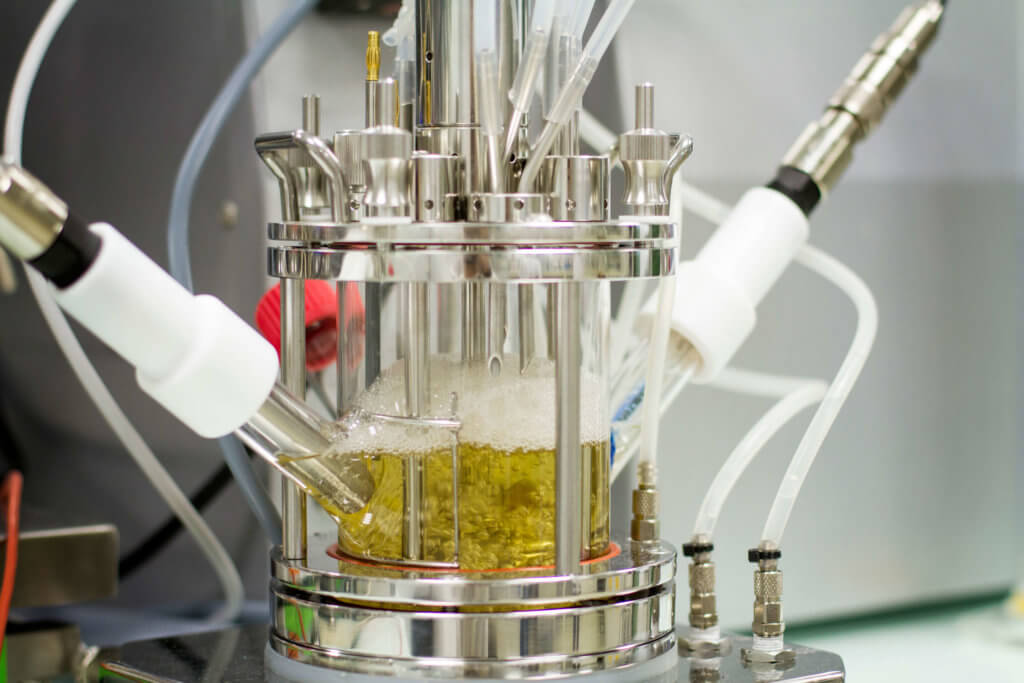
Carbios, start-up française basée à Clermont-Ferrand, a développé un procédé de dépolymérisation inédit basé sur l'action d'une enzyme qui décompose les plastiques PET en leur substance (monomère) d'origine.
Après séparation et purification, ces monomères peuvent être réutilisés dans la fabrication de PET.
Le recyclage dit « mécanique » est une technologie éprouvée qui a permis d’atteindre en France un taux de recyclage de 57% des bouteilles et flacons en PET et PEHD. A partir d’un emballage en plastique, post-consommation, le recyclage mécanique consiste à trier, broyer, laver et fabriquer des granulés, sans modifier la structure de la matière. Cette technologie est fiable, maîtrisée, mais elle ne peut traiter que des déchets d’une certaine qualité et le plastique perd quand même une partie de ses propriétés.
Par ailleurs, les additifs, les colorants, les charges minérales qui le composent et qui apportent différentes fonctionnalités à l’emballage, ne sont pas éliminés lors du process. C’est pourquoi il faut trouver d’autres procédés.
En cherchant des voies complémentaires du côté des nouvelles technologies de recyclage issues de la R&D sur les plastiques. Elles permettent de revenir aux molécules d’origines, les monomères, et d’obtenir une matière purifiée, prête à être à nouveau assemblée (c’est le processus de polymérisation) pour former des matières plastiques. Parmi ces technologies, citons la dépolymérisation qui consiste à casser les liaisons des polymères (grâce à l’utilisation d’alcool, comme le méthanol ou le glycol, voire d’enzymes) pour revenir à l’état de monomère.
Autre solution, la dissolution : elle consiste à dissoudre une matière plastique dans un solvant spécifique puis à filtrer le mélange, le nettoyer en quelque sorte, pour obtenir une matière purifiée.
Enfin, les solutions thermiques comme la pyrolyse et la gazéification visent à traiter les plastiques par la chaleur pour les transformer en composés chimiques utilisés dans la plasturgie, ou en liquides et gaz combustibles utilisés comme carburants.
En réalité, les spécialistes savent qu’elles existent en laboratoire depuis plusieurs années, sans avoir encore vraiment percé. Mais elles ont progressé et désormais nous les regardons sous un nouveau jour : celui de l’urgence environnementale et des objectifs de recyclage plus ambitieux. Il y a 20 ans, la Commission européenne fixait l’objectif de 22% de taux de recyclage des plastiques. Aujourd’hui, on veut tendre vers 100%, en France comme en Europe. L’enjeu est de sortir ces technologies des laboratoires et de valider leur faisabilité à grande échelle.
Oui, ça bouge partout dans le monde, de l’Allemagne au Canada, en passant par le Japon… et en France, où nous avons deux porteurs de projets prometteurs, Carbios et l’IFP Energies Nouvelles (IFPEN). L’un des objectifs du Forum que nous organisons avec EEQ est d’avoir une vision à jour des projets en cours à l’échelle mondiale et d’identifier les technologies d’avenir qui permettront de passer à l’échelle industrielle. Nous visons la production de dizaines de milliers de tonnes de matière.
Si les technologies avancent, l’intérêt des acteurs industriels et notamment des grands producteurs de polymères aussi ! Le contexte réglementaire et sociétal ainsi que l’extension des consignes de tri à tous les emballages en plastique ont accéléré les travaux de Recherche et Développement. Par exemple, sur son site de Carling (67) qui produit 240 000 tonnes de polymères par an, Total développe le recyclage du polystyrène par dissolution, avec la collaboration de Citeo, Syndifrais, Danone et Saint-Gobain ; c’est une avancée remarquable.
Citeo est un facilitateur et un accélérateur. Nous sommes engagés à créer les conditions économiques pour trouver des solutions pour 100% des emballages en plastique.
Avec ce Forum, nous mettons en relations et permettons les échanges entre porteurs de projets, investisseurs et industriels, nos clients. Notre mission est de les informer sur les avancées et perspectives et de leur permettre de se positionner sur ces nouvelles matières plastiques recyclées. Beaucoup d’entre eux se sont déjà engagés à intégrer plus de recyclé dans leur production pour mieux contribuer à l’économie circulaire. Pour accélérer cette dynamique collective, nous explorons les nouvelles filières de recyclage et les débouchés, comme nous l’avons fait il y a 25 ans avec le PET, le plastique des bouteilles de boissons, qui est aujourd’hui une filière robuste et efficace, au plan économique et environnemental.
Enfin, il est essentiel d’améliorer la qualité de la matière entrante dans les process de recyclage. Nous ferons prochainement évoluer certains standards en centre de tri pour atteindre la meilleure qualité possible et nous poursuivons les efforts d’éco-conception sur les emballages dont le recyclage reste à développer.